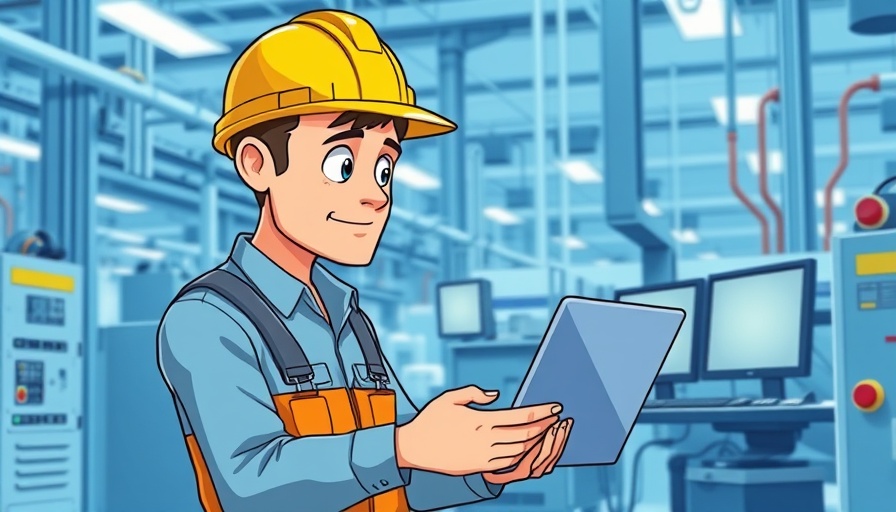
Understanding Equipment Downtime: A Necessity for Every Business
Equipment downtime is an inevitable part of running any business—one that can significantly impact your bottom line. Despite advancements in technology, even the most reliable machines can face interruptions that compromise productivity. A 2023 survey highlighted that over 3,215 industrial businesses prioritized reliability as a critical factor when acquiring new equipment. This speaks to an essential strategy that every business owner must prioritize as they work to remain competitive in their respective fields.
The Essential Role of Risk Audits
Conducting a thorough risk audit is pivotal in uncovering potential threats to your operational efficiency and profitability. Old machinery often surfaces as a major red flag; while vintage equipment may hold nostalgic value, they’re frequently more prone to malfunctions. Challenges in finding replacement parts or technicians to repair outdated models can lead to extended downtimes.
The solution? Embrace modern upgrades. Many companies are opting for newer, more dependable equipment that not only enhances productivity but also promotes employee safety and energy efficiency. When evaluating equipment, align your choices with your operational needs, factoring in how long you intend to keep each piece of machinery in service.
The Power of Tracking Downtime Events
Success hinges on your ability to measure key metrics effectively. Data collection is the backbone of operational management, allowing you to identify and rectify areas experiencing excess downtime. Digital transformation offers numerous tools for gathering this vital information. Automate where possible to alleviate the burden on staff, leading to more accurate reporting.
Tracking downtime events involves logging the duration, reason for the downtime, and specifics about the equipment and personnel involved. This comprehensive approach not only aids in understanding current issues but can inform future strategies to mitigate similar incidents.
Preventive Maintenance for Proactive Management
Regular maintenance routines are essential, yet many organizations fail to adapt their schedules based on actual equipment usage or conditions—a primary contributor to unexpected downtime. A proactive approach, where maintenance is performed based on operational hours rather than fixed calendar dates, can streamline performance and increase machine longevity.
While this might initially increase scheduled maintenance, the benefit of preventing equipment failure far surpasses the risks associated with reactive maintenance. Not only does it enhance safety for your team, but it also improves overall productivity, especially during peak business periods when unplanned failure could spiral operational costs.
The Importance of Operator Competency Training
The impact of human factors cannot be overstated in the reliability of equipment. Well-trained operators possess the knowledge required to utilize machinery efficiently, reducing the risk of accidental damages that could lead to downtime. Businesses must invest in training programs that enhance operator skills, empowering your workforce to handle machines correctly and effectively.
Creating a structured training process for your operators not only ensures familiarity with machines but also builds confidence that directly correlates with operational efficiency. The outcome? Reduced trials and errors, resulting in better management of machine usage and a decrease in unplanned downtimes.
Concluding Thoughts: Take Charge of Your Equipment Management
Understanding and managing equipment downtime is a continuous challenge that demands proactive strategies and informed decision-making. From conducting risk audits and tracking downtime events to enacting preventive maintenance and investing in operator training, these strategies collectively empower businesses to lessen downtime and maximize productivity.
As leaders, it's vital to remain engaged with innovations that can streamline operations. By adopting these strategies, you not only fortify your bottom line but also foster a safer, more efficient working environment. Don’t wait for another unplanned pause—start implementing these practices today to see transformative results in your operations.
Write A Comment